Seit der Gründung charakterisiert die ungebrochene Entwicklung unser Unternehmen. Trotz jeder externen Schwierigkeit stehen wir unseren Partnern mit unseren kontinuierlichen Entwicklungen und die Verbreitung unserer angewandten Technologien zur Verfügung.
Die immer steigernden Kundenansprüche und unser immer erweitertes Portfolio erfordern, unsere Aufgaben des Produktions- und Unternehmensmanagements am effektivsten durchzuführen. Diese Effektivität wird nicht nur durch die regelmäßige Erweiterung des Standortes und die steigende Anzahl unserer Angestellten, sondern auch durch die ehrenhafte Anerkennung von unseren Partnern bewiesen.
Unser Ziel ist, mit der Verwendung unserer bisherigen Erfahrungen weiter auf dem begonnenen Weg zu gehen, mit dem Zweck weiterhin wichtige Partner für unsere Auftraggeber sein zu können. Es ist wichtig für uns, dass unsere Produkte bei dem Nutzer Sicherheit und Vertrauen erweckt und gute Nutzbarkeit und die Nachricht von Komfort und Ästhetik aus sich strahlt.
1988 DIE ANFÄNGE …
Unser Unternehmen ist in der Garage unseres im Zentrum von Gemeinde Fajsz stehenden Einfamilienhauses entstanden ist. Anfangs produzierten unsere Familienmitglieder zusammen mit einigen Mitarbeitern Ersatzteile für Landwirtschaftsmaschinen, Möbelbeschläge in kleiner Serie. Wir wurden Zulieferant erster Wahl für die Fabrik von Ungarischer Suzuki in Esztergom seit deren Gründung im Jahr 1992.
1993 FIRMENGRÜNDUNG: DIE UMWANDLUNG DES BEREITS BESTEHENDEN UNTERNEHMENS IN EINE GESELLSCHAFT
Während der Zusammenarbeit mit einem der größten Unternehmen der Autoindustrie der Welt lernten wir die japanische Arbeitskultur, die Effektivität und das KAIZEN kennen, was wir auch bei unserer Produktion verwendeten und auch weiterentwickelten.
Unsere Familie setzte ihre Tätigkeit in Zusammenarbeit der ersten und zweiten Generation als Wirtschaftsgesellschaft fort.
2001 GROSSER SCHRITT: NEUER FABRIKSTANDORT – KLEINMASCHINENHALLE
Die Steigerung der Anzahl der Aufträge und die Erhöhung der Qualitätsanforderungen machten die vollständige Erneuerung unaufschiebbar. Aus größtenteils eigener Kraft bauten wir eine Betriebshalle und ein zentrales, zweigeschössiges Bürohaus mit Verhandlungsräumen, Büros, Ankleideräumen mit einer Grundfläche von 1.600 m2 auf einem Paprikafeld in der Nähe von Gemeinde Fajsz.
In der damals modernsten, den Arbeitsschutz-, Produktions- und Funktionserwartungen entsprechenden Betriebshalle stehen heute unsere Pressmaschinen von kleineren Leistung und die Arbeit läuft in zwei Schweißräumen. In dieser Halle führen wir die Kontrolle, die Qualitätsprüfung und die Vorbereitung der Auslieferung der Fertigprodukte separat durch.
2004 PROGRESSIVER PRESSBETRIEB UND LAGERGEBÄUDE
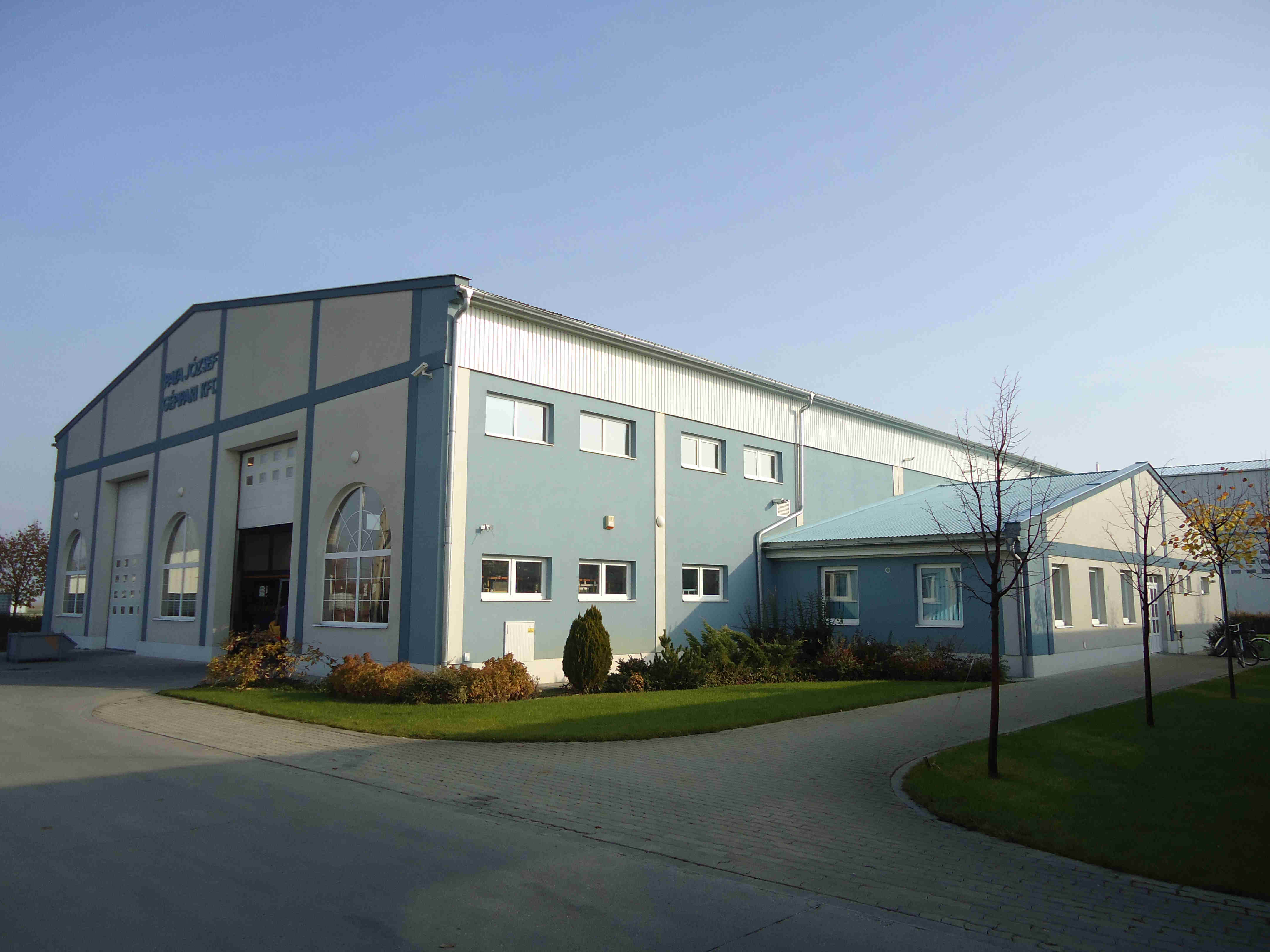
Unsere erste Halle erfüllte unser Bedarf an Produktionskapazität drei Jahre lang, aber wir mussten der Änderung unseres Auftragsvolumens verfolgen, so wurde die Erweiterung des Standortes unaufschiebbar. Mit dem Kauf von neuen Grundflächen konnten wir unser freies Betriebsgelände erweitern, im Jahr 2014 bauten wir eine Betriebshalle mit einer Grundflächen von 700 m2 für progressive Pressmaschinen und im Jahr 2005 ein Lagergebäude auch mit einer Grundflache von 700 m2 auf.
2007 PRESSBETRIEB FÜR GROSSMASCHINEN UND KANTINE
Nach weiteren drei Jahren realisierten wir unseren alten Plan: wir bauten ein Logistiklager mit einer Grundfläche von 700 m2 und eine Betriebshalle mit einer Grundfläche von 1.200 m2 auf. Hier unterbrachten wir die Vorzeigestücke unserer Firma, die japanische Servo-Pressmaschine KOMATSU mit einer Pressleistung von 200 Tonnen bzw. die von der italienischen Firma ZANI SPA nach unseren Ansprüchen geplanten und produzierten Pressmaschinen mit einer Leistung von 300, 400 und 500 Tonnen. Auf die zuletzt genannten Maschine montierten wir auch Roboterarme.
Über die Funktion der Roboter-Manipulatoren kann man den in unserer Fabrik aufgenommenen Kurzfilm von Flexman Robotics anschauen.
Für unsere Mitarbeiter bauten wir Entspannungs- und Sozialräume in unseren Produktionshallen aus, aber der Ausbau einer zentralen Kantine wurde unaufschiebbar. Unsere auf dem nur für diesen Zweck gekauften Grundstück aufgebaute Kantine mit warmer Küche bietet bequemes und kultiviertes, tägliches Essen für 60 Personen Platz.
2010 EINFÜHRUNG DER ROBOTERTECHNOLOGIE: HALLE DER SCHWEISSROBOTER – SCHWEISSROBOTERZELLEN
Mit Versuchscharakter stellten wir die von REHM Kft. hergestellte Schweißroboteranlage vom Typ YASKAWA MOTOMAN bereits im Jahr 2009 in die Produktion ein, was genauer und nicht zuletzt in besserer Qualität und effektiver das Punktschweißen unserer in Massenfertigung hergestellten Produkte durchführt.
Die Einführung der Robotertechnik brachte vielversprechende Ergebnisse mit sich, aus diesem Grund bauten wird trotz der ab 2008 Ungarn und besonders die Autoindustrie wesentlich betreffenden Wirtschaftskrise mit einem mutigen Schritt unsere Betriebshalle für Schweißen mit einer Grundfläche von 600 m2 auf.
Im neuen Gebäude stellten wir zwei neue Schweißroboter vom Typ YASKAWA MOTOMAN neben den automatischen Schweißgeräten von REHM Kft. in die Produktion ein. Im Jahr 2013 stellten wir auch einen neuen Roboter neben bereits bestehenden drei in den Betrieb ein.
2012 EINFÜHRUNG DER SPITZENTECHNOLOGIE: ZANI
-HALLE MIT KRAN
Der japanische Begriff „KAIZEN“ bedeutet „die kontinuierliche Entwicklung für eine bessere Zukunft”. Infolge dieses Prinzips entschlossen wir über den Bau einer die modernste Technologie verkörpernden Produktionshalle im Jahr 2011. Unsere Pläne wurden am Ende 2012 realisiert: ein Fabrikgebäude mit einer Grundfläche von 1000 m2 und einer Höhe von 11 Meter ist aufgebaut worden, das nach der dort platzierten italienischen Pressmaschinenflotte „ZANI“-Halle genannt wurde.
Samt der bereits bestehenden, mit Roboter-Manipulator versehenen Pressmaschinen mit einer Kraft von 500 Tonnen wurden wir mit den neu gekauften ZANI-Pressmaschinen mit Pressleistung von 400, 500, 630 und 1.200 Tonnen auch zur Produktion von größeren und komplizierteren Autoersatzteilen fähig.
In der Mitte unserer Pläne steht die Beschaffung von weiteren Pressmaschinen von großer Leistung und in der Größe eines Tisches, sowie Roboter-Manipulatoren und Transferanlagen.
Die Maschinen werden mit einem Laufkran mit einer Leistung von 12,5 Tonnen, sowie einem in den Boden versenkten Förderbandsystem für Abfallaustragung bedient.
Auch ab diesem Jahr werden die hinteren elektrischen Fensterheber für SUZUKI Fahrzeuge in der Wiege unseres Unternehmens, im Zentrum von Fajsz als Subzulieferant von JOHNAN UK produziert und montiert.
Dieser technologische Schritt verbirgt weitere Herausforderungen im Leben unseres Unternehmens und weitere Entwicklungsmöglichkeiten in sich.
2015 STANDORTERWEITERUNG – TRANSFERTECHNOLOGIE
Unser vor acht Jahren übergebenes Gebäude mit der Kantine entwickelten wird mit spektakulären architektonischen Lösungen zum Gemeinschaftsraum: auch ein Veranstaltungsraum und eine Ausstellung mit der Geschichte unserer Firma wurde hier unterbracht.
Die regelmäßige Wartung, Pflege und angemessene Aufbewahrung unserer wesentlichen Wert verkörpernden Produktionswerkzeuge sichern, dass wir jederzeit am wirtschaftlichsten fehlerfreie Produkte herstellen können. Die grundlegenden Bedingungen dafür sind die fachkundigen Hände und die fachgerechte Aufbewahrung.
Zur Realisierung der obigen Anforderungen begannen wir mit dem Aufbau unserer neuen Lagerhalle, in der unsere Werkzeuge, Produktionsmittel geordnet und sicher aufbewahrt werden und dadurch wesentliche Bereiche in unseren Produktionshallen befreit werden.
Wir entwickelten zwei Pressmaschinen in Zusammenarbeit mit ZANI SPA mit der von NORDA SPA gelieferten Transferanlage weiter, dessen Zweck nicht das Ersetzen von menschlichem Know-how war, sondern die Ablösung der physischen Arbeit und die Sicherung der kontinuierlichen, fehlerfreien Produktion wichtig waren. In der Pressmaschine leitet diese Anlage die Ersatzteile zwischen den Produktionswerkzeuge weiter, was die Effektivität der Pressmaschine vervielfacht.
TECHNOLOGIE-UPGRADE 2019 – LASERSCHNEIDEN, LICHTBOGENSCHWEISSEN UND TIEFZIEHEN
Was wir in den letzten drei Jahrzehnten gelernt haben, ist, dass wir neben dem Pressen und Schwingen von Autoteilen neue Methoden in die Produktion einbringen müssen.
Während dieser Jahre der Arbeit kam die Nachfrage nach dem Schneiden und Biegen von Blechen in steigender Zahl zurück.
Nach langer Planung stellten wir den Entwurf einer neuen Halle mit neuen Maschinen zusammen, den wir in knapp einem Jahr erfolgreich umsetzten – teils aus eigenen Mitteln, teils durch Ausschreibungen.
Unsere neue 580 m2 große Halle ist mit der neuesten Luftwechseltechnologie ausgestattet, mit einem Laufkran mit einer Kapazität von 12 Tonnen, zwei FANUC Punktschweißrobotern, einem FANUC Lichtbogenschweißroboter, einer SALVAGNINI Laserschneidmaschine und einer SALVAGNINI Biegemaschine. Außerdem haben wir hier vier Inverterschweißmaschinen und ein 3D-Präzisionsmesslabor untergebracht.
In dieser Halle werden die Teile für die neuen Hybridautos gefertigt und montiert. Außerdem produzieren wir hier große Karosserieteile, die besonderes Know-how und Sicherheit erfordern.
Um diese komplizierten Teile herstellen zu können, haben wir dieses Jahr eine neue hydraulische Presse von GALDABINI angeschafft.
2020 QUALITÄT UND GENAUIGKEIT: VERPACKUNGSHALLE UND WARENWIRTSCHAFT
Aufgrund der positiven Entwicklung unserer Produktionskapazität in den letzten drei Jahren mussten unsere Verpackungsanlagen erweitert werden.
Unser Mangel an sicherem und zuverlässigem Verpackungsraum bedrohte nun die Pünktlichkeit und die Qualität unserer Produkte.
Es lag in unserem besten Interesse, dieses Risiko zu lösen und zu minimieren. Angesichts der Beschränkungen der COVID-19 in Ungarn haben wir erfolgreich eine 530 m2 große Verpackungshalle mit Regalen gebaut, die 180 Behälter aufnehmen können. Hier können wir die neuen großen Metallteile bis zum Versand sicher lagern.
Um den strengen Vorschriften der Industrie in Bezug auf Produktsicherheit und Qualität gerecht zu werden, haben wir ein neues Labor zur Messung der von uns hergestellten Teile, einschließlich der lichtbogengeschweißten Teile, entwickelt.
In diesem Jahr hat unser Unternehmen erfolgreich ein neues ERP-System eingeführt, so dass wir die Planung von Produktion, Lagerbestand, Personalangelegenheiten und Finanzen effektiver und sicherer überwachen können.
Auch in diesem Jahr haben wir unsere Roboterschweißtechnologie und -kapazität durch die Installation von zwei FANUC Punktschweißzellen weiter ausgebaut.